Effect of Alloying Elements on Machinability
- Josephine
- 6 days ago
- 2 min read
Alloying elements are added on purpose to influence the mechanical and thermal properties of the material in a targeted manner. The following describes the influence of some important alloying elements on the machinability of steel.
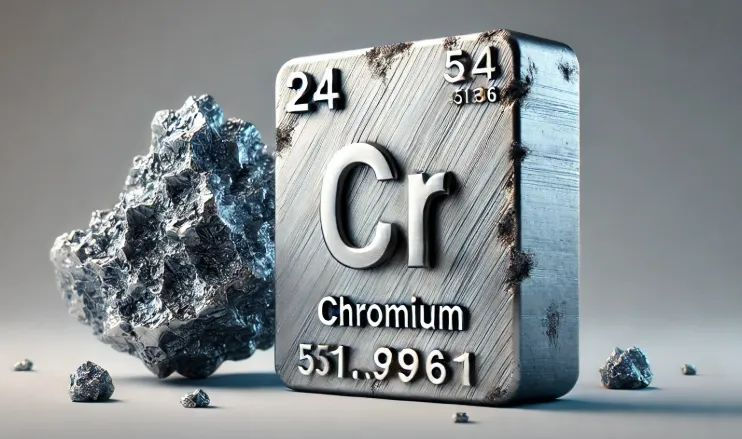
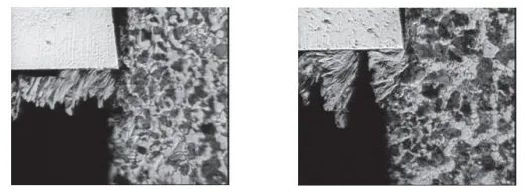
Left: 0.021% sulfur → thin ribbon chips
Right: 0.17% sulfur → increased chip brittleness
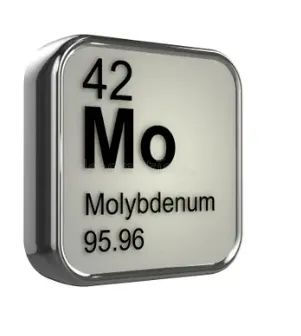
Chromium and molybdenum increase the hardenability of steel and therefore affect the machinability of carburized and quenched and tempered steels through microstructure and strength. In steels with a high carbon content or alloying components, these elements form hard special carbides and mixed carbides, which reduce machinability. The same applies to tungsten.
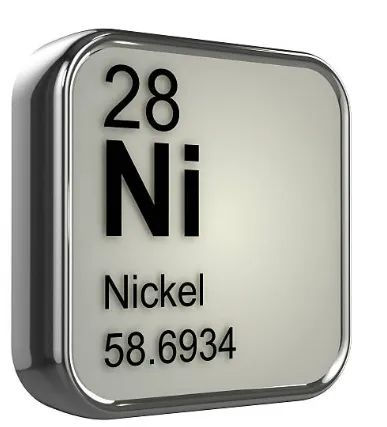
Nickel also affects the strength of steel and increases its toughness. In general, this reduces machinability, especially in austenitic nickel steels (especially when the nickel content is high).

Silicon increases the strength of ferritic steels and forms hard silicon oxide the silicate, inclusions in combination with aluminum. This leads to increased tool wear.

By adding phosphorus, short chips can be formed. Up to 0.1% phosphorus has a positive effect on machinability. Higher phosphorus contents lead to better surface quality but also to increased tool wear.

Even small additions of titanium and vanadium lead to a significant increase in the strength of the steel. Due to the severe grain refinement, the results for cutting forces and chip formation are worse.
Sulfur has a very low solubility in iron but forms stable sulfides in the steel depending on the alloy composition.
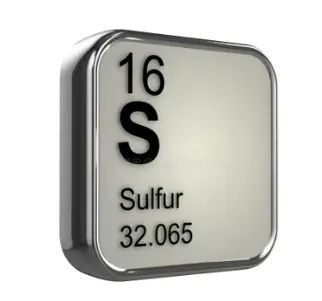
Manganese sulfide MnS is the desired sulfide because it has a positive effect on machinability -short and brittle chips, less chip edge formation, improved workpiece surface. By varying the sulfur content in the steel, chip breaking and burr formation during machining can be substantially influenced.
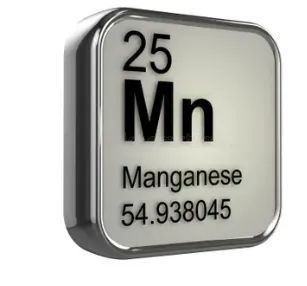
Manganese increases the hardenability of steel and the strength of the steel. Since it readily combines with sulfur, manganese forms sulfides with sulfur. For steels with low carbon content, manganese content up to 1.5% is beneficial due to improved chip formation. However, at high carbon contents, it increases tool wear and has a negative impact on cutting.
Lead has a relatively low melting point and is present in iron as submicroscopic inclusions. During cutting, a protective lead film forms between the tool and the workpiece material, which reduces tool wear and reduces specific cutting forces. The chips become short and brittle.
Comments